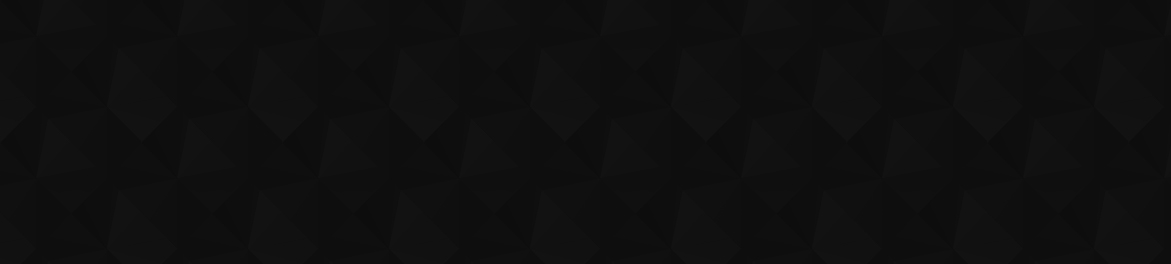
- Видео 290
- Просмотров 2 102 748
Additive Manufacturing Media
США
Добавлен 17 июн 2015
Additive Manufacturing is the media brand devoted to industrial applications of 3D printing. Our editors travel the world exploring how additive manufacturing is transforming production, and how real manufacturers are using 3D printing to make end-use production parts and tooling in many industries. One of our productions is The Cool Parts Show, an ongoing series highlighting innovative components and products made possible through 3D printing. (Have one? Email coolparts@additivemanufacturing.media)
For manufacturers succeeding with additive today, and those who might be using it tomorrow: Our reporting is for you. Subscribe on RUclips, follow us on social, sign up for our magazine or newsletter, and keep in touch!
Twice a week, AM editors share insights in The BuildUp. See what they're saying: gbm.media/TBU
Additive Manufacturing is published by Gardner Business Media. Sister brands: Modern Machine Shop, MoldMaking Technology, Plastics Technology and CompositesWorld.
For manufacturers succeeding with additive today, and those who might be using it tomorrow: Our reporting is for you. Subscribe on RUclips, follow us on social, sign up for our magazine or newsletter, and keep in touch!
Twice a week, AM editors share insights in The BuildUp. See what they're saying: gbm.media/TBU
Additive Manufacturing is published by Gardner Business Media. Sister brands: Modern Machine Shop, MoldMaking Technology, Plastics Technology and CompositesWorld.
Laser Powder Bed Fusion With Multiple Materials
In laser powder bed fusion (LPBF), applying multiple materials separately within the same build seems as though it should be impossible. The “bed” of the powder bed machine is an undifferentiated mass of powder, offering no capacity to segregate separate materials.
Schaeffler Aerosint offers a system that brings this segregation to LPBF machines. It works by delivering different materials each to individual drums above the powder bed, with these drums using negative pressure to precisely lay material onto an in-process build.
Penn State University’s Center for Innovative Materials Processing through Direct Digital Deposition (CIMP-3D) is experimenting with applications of this system for bu...
Schaeffler Aerosint offers a system that brings this segregation to LPBF machines. It works by delivering different materials each to individual drums above the powder bed, with these drums using negative pressure to precisely lay material onto an in-process build.
Penn State University’s Center for Innovative Materials Processing through Direct Digital Deposition (CIMP-3D) is experimenting with applications of this system for bu...
Просмотров: 2 310
Видео
3D Printed Titanium Replaces Aluminum for Unmanned Aircraft Wing Splice | The Cool Parts Show Ep.72
Просмотров 27 тыс.День назад
Aircraft makers applying 3D printing processes to manufacture plane components often begin with less critical parts first, then proceed to more vital parts as confidence builds. But with General Atomics’ introduction of directed energy deposition (DED) to part production, the company began with a part that could not be more critical to flight. DED via the Rapid Plasma Deposition process from No...
3D Printed PEEK Spine Implants in Production | The Cool Parts Show Bonus
Просмотров 4,6 тыс.14 дней назад
In episode #63 of The Cool Parts Show, we learned how medical device manufacturer Curiteva is applying a proprietary 3D printing process to produce spine implants from PEEK. Polyether ether ketone offers mechanical properties similar to bone making it attractive for this application, and machined and molded PEEK implants have been in use for years. But Curiteva’s process, Fused Strand Depositio...
Harder, Longer-Lasting Brake Discs via Carbide Deposition
Просмотров 1,6 тыс.21 день назад
Etxetar and Talens are developing an additive manufacturing process utilizing precise laser metal deposition to mass-produce automotive brake discs, incorporating tungsten or titanium carbide layers for enhanced wear resistance. Spanish machine tool builder Etxetar, along with its sister company, laser deposition specialist Talens, together are working with a major auto producer to develop a pr...
Robot Repairs Giant Wind Power Shafts Using 3D Printing
Просмотров 1,8 тыс.Месяц назад
In Rentaria, Spain, Peter Zelinski got to see a major, successful system for large-scale component repair via additive manufacturing. A maker of wind power equipment needed a more effective way to repair its systems’ main shafts. Cold spray sometimes works to repair worn bearing areas on the shafts, but not reliably so. Scrapping a shaft and replacing it represents an expense of 140,000 euro - ...
3D Printed NASA Thrust Chamber Assembly Combines Two Metal Processes | The Cool Parts Show
Просмотров 10 тыс.Месяц назад
When we talk about spacecraft, we are largely talking about propulsion. About 70% of the cost of a spacecraft, along with considerable manufacturing lead time, is attributable to the propulsion system alone. That means the chance to streamline the design and production of this system offers the chance to deliver dramatic time and cost savings in spacecraft manufacturing. NASA’s Rapid Analysis a...
Binder Jetting Production Workflow at Freeform Technologies
Просмотров 2,2 тыс.Месяц назад
Freeform Technologies of St. Mary’s, Pennsylvania, is a contract manufacturer relying on various processes employing powder metal and sintering - most notably binder jetting. Thanks in part to a recent acquisition that significantly expanded its capacity, the company now runs 22 binder jetting machines. In a recent article for Additive Manufacturing Media, we reported on Freeform Technologies a...
Ergonomics and Economics of Really Big Laser Powder Bed Fusion
Просмотров 2 тыс.2 месяца назад
As laser powder bed fusion (LPBF) machines get larger, they introduce new challenges when it comes to the ergonomics and economics of 3D printing metal parts from powder. This video filmed at CIMP-3D, the Center for Innovative Materials Processing through Direct Digital Deposition located at Penn State University, looks at a large-format “factory” built around a 3D Systems DMP500 3D printer wit...
3D Printed Bioreactors Enable Cell Growth | The Cool Parts Show Ep. 70
Просмотров 4,3 тыс.2 месяца назад
The Southwest Reasearch Institute is using 3D printing to more efficiently grow billions of cells! By 3D printing bioreactor scaffolds, they are able to create unique geometries with larger surface areas leading to more cell growth. One drawback to this method is that it generates extremely large file sizes. Implicit modeling offers a potential solution. One of the next frontiers in medicine is...
What is MoldJet? Sinter-Based Additive Manufacturing at APG
Просмотров 2 тыс.2 месяца назад
Alpha Precision Group (APG) in Ridgway, Pennsylvania, has a history of manufacturing parts through powder metallurgy. Along with conventional techniques including press and sinter and metal injection molding (MIM), the company now uses a collection of metal 3D printing techniques as well including binder jetting, bound metal deposition (BMD) and now MoldJet. The MoldJet process developed by Tri...
3D Printing Means Faster Lead Time for This Valve Component | The Cool Parts Show Ep.69
Просмотров 6 тыс.3 месяца назад
Baker Hughes supplies industrial valve components including a line of variable resistance trim stacks, used to alleviate cavitation when installed in reciprocating valves. In the past, these parts have literally been stacks-pieces of metal drilled, stacked and brazed together to create the tortuous geometry that counters pressure drop and prevents cavitation bubbles from forming. The manufactur...
Aircraft Ducts 3D Printed in Composite Instead of Metal | The Cool Parts Show Ep.68
Просмотров 6 тыс.4 месяца назад
Aircraft Ducts 3D Printed in Composite Instead of Metal | The Cool Parts Show Ep.68
Intelligent Layering Metal 3D Printing at 3DEO
Просмотров 2,1 тыс.4 месяца назад
Intelligent Layering Metal 3D Printing at 3DEO
3D Printed Hypersonic Missile Nose Cone Made on Hybrid CNC Machine
Просмотров 2 тыс.5 месяцев назад
3D Printed Hypersonic Missile Nose Cone Made on Hybrid CNC Machine
This 3D Printed Titanium Part Protects IndyCar Drivers | The Cool Parts Show #67
Просмотров 3,7 тыс.5 месяцев назад
This 3D Printed Titanium Part Protects IndyCar Drivers | The Cool Parts Show #67
Introducing The Cool Parts Show: All Access
Просмотров 3795 месяцев назад
Introducing The Cool Parts Show: All Access
3D Printing Crash Lands on Earth in NASA's Mars Sample Return Mission | The Cool Parts Show Bonus
Просмотров 4,2 тыс.5 месяцев назад
3D Printing Crash Lands on Earth in NASA's Mars Sample Return Mission | The Cool Parts Show Bonus
3D Printed Drone Bird Flies Like a Real Bird | The Cool Parts Show #66
Просмотров 17 тыс.6 месяцев назад
3D Printed Drone Bird Flies Like a Real Bird | The Cool Parts Show #66
How Data Makes DED a Trustworthy Alternative to Casting
Просмотров 2 тыс.6 месяцев назад
How Data Makes DED a Trustworthy Alternative to Casting
Faster Laser Powder Bed Fusion: 3D Printing While Recoating | Formnext 2023
Просмотров 2,7 тыс.7 месяцев назад
Faster Laser Powder Bed Fusion: 3D Printing While Recoating | Formnext 2023
3D Printing Elastomers onto Textiles | Formnext 2023
Просмотров 1,9 тыс.7 месяцев назад
3D Printing Elastomers onto Textiles | Formnext 2023
Directed Energy Deposition 3D Printing at Large and Small Laser Sizes | Formnext 2023
Просмотров 2,4 тыс.7 месяцев назад
Directed Energy Deposition 3D Printing at Large and Small Laser Sizes | Formnext 2023
Using Density to Confirm a 3D Printed Part is Solid | Formnext 2023
Просмотров 1,4 тыс.7 месяцев назад
Using Density to Confirm a 3D Printed Part is Solid | Formnext 2023
Liquid Metal + Laser Wire 3D Printing | Formnext 2023
Просмотров 3,3 тыс.7 месяцев назад
Liquid Metal Laser Wire 3D Printing | Formnext 2023
8 Cool 3D Printed Parts From Formnext 2023 | The Cool Parts Show #65
Просмотров 8 тыс.7 месяцев назад
8 Cool 3D Printed Parts From Formnext 2023 | The Cool Parts Show #65
Reinforcing 3D Printed Parts with Continuous Fiber Injection Process | Formnext 2023
Просмотров 3,3 тыс.7 месяцев назад
Reinforcing 3D Printed Parts with Continuous Fiber Injection Process | Formnext 2023
Denser Ceramic Parts 3D Printed Using Nanoparticles | Formnext 2023
Просмотров 1,5 тыс.7 месяцев назад
Denser Ceramic Parts 3D Printed Using Nanoparticles | Formnext 2023
Mobile Robot Unloads 3D Printer Farm | Formnext 2023
Просмотров 1,4 тыс.7 месяцев назад
Mobile Robot Unloads 3D Printer Farm | Formnext 2023
3D Printing with Liquid Aluminum | Formnext 2023
Просмотров 9 тыс.7 месяцев назад
3D Printing with Liquid Aluminum | Formnext 2023
3D Printed Ductile Spikes for Better Sound Quality | The Cool Parts Show Bonus
Просмотров 1,8 тыс.7 месяцев назад
3D Printed Ductile Spikes for Better Sound Quality | The Cool Parts Show Bonus
Isn't aermet100 as good or better than titanium by weight? but perhaps it's at least as hard to work with. Maybe some kind of magnetic field shaping could refine the process so it isn't so beady.
A retired Engineer I have been 3D Printing for over 8 years to make parts for my 1950 Model Trains. I worked in Medical, Aerospace and Automation systems when working. I could see the possibilities to get the heat on these exotic materials was a problem. Then I saw concrete printing house frames. And FFP is making energy from Plasma Arcs on a small scale. Plasma ??? Now I see this and it is heart warming to see Plasma controlled to melt Titanium ina highly more efficient and effective process to use less material in waste and speed up production of critical parts. Very good work and I hope is able to be miniaturized for space station operations to fabricate spares as needed from rolls of wire. Point of use Production meets Plasma Deposition it a very good thing. Add some AI to the control logic for perfect print 100% of the time and get part Cad data for every viable part required, beam up new improved part shapes as needed, wow. D
This could be incredible for warfare, no? Silent and getting confused with real birds..
This is of course stupid! Unmanned aircraft are not intended to do acrobatics.
The parts aren’t strictly for drones.
Thanks for sharing this.
NOT ENOUGHT MATERIAL IN PLANET TO REPLACVE ALU.. wtf you lie baout..
Why is this dude so animated ?
Couldn't you just weld titanium to make that rough shape more or less and then mill it
You want to minimize welding in airframe components because you cannot guarantee that the weld is as strong as a solid block and causes inconsistent material properties that can lead to fracture caused by metal fatigue. Welding also may cause warpage of the part. In this case you minimize labor, need no fixturing and it is made in 1 step. You are adding multiple steps if you say welded plates together. You have to cut the plates (very expensive in titanium), fixture them, weld them, test the welds for consistency and penetration dye, then fixture in a machine and mill it (extremely expensive). This is as simple as pressing go on the machine and then voila there is your part.
@@letsbuildit6954the parts Norsk makes do still need finish machining, but yeah other than that, spot on.
Why not using a single piece construction, since in this design also we have to put a plate on top, fasten in, put a gasket and then hope that it won't leak.
Alot of buzzwords flying around.
Good idea but the most of the titanium dont come from russia , oh boy i know who come to 🕌🕌🕌⌛copy the tech....
Surely one could separate out the two materials in the bed by their material properties, such as with a magnet or a centrifuge. I dont know if it would be worth the effort, but it must be possible, no?
Plus’s and minus’s but definitely a step forward I think 🤔 Could be used to print different graded material sizes too but more for a single material run…. Just my skying it😂
ruclips.net/video/ptlhgFaB89Y/видео.html This could make a small fusion reactor, because the Superconductor YBMC is about the same melting point of copper, that takes expensive Rebco tape and turns it into a simple build. It makes a complex stellarator into an inexpensive print. A reactor could be as small as a toaster and so simple it could be disposable. It would be nice if it could also print the tungsten wall lining, but allot of laser power required. Chanels for liquid helium, and liquid Lithium would be simple to build this way. Since Reboco like tape can be badly damaged and still not quench it is unlikely Neutrons would damage the superconductors. Even if it did the blankets were intended to be replaced every two years, why not make the whole reactor cheap, small and disposable. It would only need to last a week to be of military value, no battery recharging needed. Robotic tanks could easily establish a path and break front lines.
Titanium from Rusia?!
Not eney more and it seems that new suplier has made a co.kup. Big aircraft manufacturers haw sounded the alarm that titanium parts are not the grade they shoud be. Hm, they didnt hear of metal testing before use as it seems...
All drones are the size of small planes
Нифига.
Not being able to reuse the unused powder would greatly increase costs.
This process looks like an analog for color xerographic (electrophotographic) printing, but with different metals instead of toner.
This technology can be used to make not only radiators, or heat exchange tubes. I think it can print thermal barriers or composite details with ceramic structures inside. And if you can select materials correctly, you can do this details monolythic after firing and diffusion.
I like this idea. Is it possible to recycle the powder? What can you do with used powder?
Copper & titanium powder can probably be separated by passing it over a magnet a few times.
@@disposabull did you hear about Gas centrifuge?
That part still needs to be (finish) machined, that was stated but perhaps not that clearly put. Obviously much less machining and far few chips that starting from a billet.
cool, hope aluminum and energy problems will be solved soon and I can print myself a liveaboard katamaran fully electrical covered with solarpanels like a greenhouse, powering all the appliances and storing excess in batteries and maybe hydrogen for a more conventional backup
⚡️🛩️👍
This was the least impressive part made by Norsk Titanium! Norsk Titanium is the only additive manufacturing company in the world with FAA approval for making critical components such as blades for turbofan engines etc. This video missed the point an lent the ear mostly to a mediocre drone producer insted of focusing on the real story here! Sorry, but thumbs down!
Nobody wants be be a manufacturer, everyone wants to be an information company.
Talk about the part more. Point at it and explain.
A Meltio M600 machine would've been made it better imhso.
Interesting comment. Why do you think this might be the case? How long would it of taken to lay that part down on a Meltio? The wire diameter is nearly three times smaller. Remember this is a production piece. Is it possible for Meltio to lay down such a large piece efficiently?
@@78bookem I'm not sure as to how long it would've taken the Meltio M600 to lay down the same piece, but given they ability for the head to be put on a robot arm, I think it would've been able to accomplish the same task with off the shelf wire in an efficient manner. The Meltio can accomplish production pieces all the same.
As someone who literally works at Norsk making these parts, NO. It’s missing quite a few features that make depositing titanium possible for aerospace applications.
@@dubyas1989 ok like I had previously said, imhso. It's just blind love for the Meltio. Have a scintillating day! 😆
this is like that article I just read about time being hypothesized as being purely quantum, and yet an illusion, but the article never goes into a semblance of depth into the subject. just stuff like they are trying to teach a 5 year old. if all they produce is stuff that doesnt challenge the public, they will always be stuck at "dumb"
yes lets play the same stupid clips over and over. lost interest when all I was listening to was slow-talk about blah blah blah. I begin scanning ahead and all I see if the same crap : clip - someone going blahh blah blah - same clips - blah blah blah who cares? youtube is flooded with bloated crap. this just added itself to the list. I'll wait for someone else to provide pertinent information at less of a cost to my time.
Boeing 787 you say..... some of the strictest standards you say....
So cool.
Can somebody tell this guy to stop moving his hands and gesturing like this is a kindergarten class? The woman does fine. These are part manufacturing, not teaching how to participate in class
(perhaps he is Italian and you just insulted him for being himself?)
Is it possible to bond green parts together before sintering? (or repair green parts..) If so, what medium is used? Any videos on it?
any specialists here? is titanium not as problematic as in marine use? bcs of the catalyst effects destroying everything around? maybe some coating?
The properties that make Titanium desirable for use in highly demanding applications also make Ti very difficult to fabricate parts from. The Soviets wanted to make a Nuclear submarine because of these very properties "The practical problems with the design quickly became apparent and in 1963 the design team was replaced" (Wikipedia - Alfa-class submarine). The advancements described in this video offer new opportunities to revisit use of Ti in innovative ways.
Titanium is very resistant to chloride corrosion. Aluminium isn’t. Very useful for sea skimming vehicles.
Depends on grade, mix of tipes of cristals. As in steel, more strength less corrosion resistance. But for most, titanium is one of the best choices. But dont forget electrochemical corrosion, contact whit other metals.
@@ljubomirculibrk4097 Actually the highest strength iron alloys are very corrosion resistant - it is carbon content that accelerates corrosion.
So is the END PRODUCT PART - LIGHTER WEIGHT. How much lighter weight is the DED produced Titanium Part (at the same strength performance delivering part of the existing/previously used Fully forged Aluminium alloy - CNC Cut out part. 5% lighter weight 10% lighter weight 15% lighter weight 20% lighter weight 25% lighter weight 30% lighter weight 35% lighter weight 40% lighter weight 45% lighter weight 50% lighter weight 55% lighter weight 60% lighter weight 65% lighter weight 70% lighter weight 80% lighter weight 85% lighter weight 90% lighter weight 96% lighter weight 100% lighter weight > 100% lighter weight PLEASE ask the General Atomics company - to answer this question - and give answer as a reply to this comment AND update the video with the information - in the video OR in the description section OR in an additional comment by you placed at the top of the comments section OR with an updated - more information filled video at the ALL ACCESS spot on your website.
Weight change actually was not the outcome sought with this part. Volume change is more like it - titanium allows for the same strength in a part that is less bulky, and takes up less space in the complete assembly.
wow evil company
Ok, I'll bite. Why is it evil?
Damn some people have smart and interesting prozesses. I would Love to Work in Industries Like this but I feel Not experienced enough. But I am also to old to Just Switch industrys😅
The industry didn’t exist 10yrs ago, nobody has much experience. I actually work at Norsk after years of being a machinist.
@@dubyas1989 Hi, first of all thank you for encouraging me. I should maybe explain my comment a little. I am a 3d artist and have worked in a company where one of my tasks was to prepare archaeological finds for 3d printing. So I'm not completely new but I don't have enough practical experience in industrial printing and I've never been a machine operator. I would like to change but I have some responsibilities and therefore I can't start anywhere as a trainee, which means I lack the knowledge and I am not in the financial situation to build it up in a company. I am studying a lot myself but I feel like before I realy worked in a workshop on the mashines I dont feel good aplaying.
CORRECTION: In the episode, we said the new wing splice is for the SkyGuardian aircraft. That is incorrect. It was designed to requirements similar to those of the SkyGuardian, but which platform it will be used on has not been determined.
Shame there was no footage of chips flying on that additive part. If that same process can be used for Aluminium, the companies custom manufacturing race & street engines will be very interested - the materials and machining savings on an engine block or cylinder head would be massive, along with being able to print in better water galleries for coolant passage, making those engines lighters and more reliable. One-off parts, such as a replacement water pump for a historically signifigant vehicle, also drop in price. I believe the Rocket Labs "Rutherford" rocket engine is made in a similar way, as are few of the newer Small-Sat launch vehicles, along with at least one using this sort of method to print the main fuel tanks of their booster.
How come the titanium didn't change color with the heat of the plasma? It must be cool to aid in preventing warping too :)
Sure😉
The Cool Parts Show is my new favorite! You both are a dynamic duo!
Thank you both for representing the industry. The trust you have built with factory suppliers and end users, esp. defense, gives all of us inspiration to see what's possible with AD.
Thank you both for the information.
Sounds like it is more expensive than just using aluminum. I got an offer at an aerospace 3d printing company in Knoxville, TN and they only offered me $12 an hour and I have a degree and experience!!!Absolutely ridiculous and insulting! These companies cheap out on paying employees cause everything else cost so much money.
How to be an idiot without saying you are one: Example 1
Norsk takes great care of us.
They say the opposite. If you make the part from aluminum you start from a block with the overall dimensions and you have to remove 90% machining. So you are paying a lot for the raw material and a lot for the machining (time, tooling...). For big titanium parts, it is difficult to make the above in a cost effective manner. But if you start with a preform, the case is completely different. In this same channel, there's an example at NASA of big parts being made in titanium thanks to additive manufacturing. Why would they change the part and the processes if it is not to save in costs? Look for a company where they value you more, good luck!
12$ an hour is hilarious… the girl that pours my coffee at dunks down the street from me gets 18$ not including tips 😀
truly amazing
Very impressive part and tech. Must have a protective atmosphere for the wing splice deposition, the smaller part shown earlier had some oxidation not present on the big part.
Please I needs your Email and also Erik Erbe for PhD supervisor. I'm PhD candidate In material Engineering......
i was here and there. Aqui y alla....xD
Yes they do it for other purposes afcourse budget unlimited 😢😂
I would love to see how they test the piece for it's ability to withstand constant vibration for the expected lifespan of the aircraft and also would like to know how the part is fixed in position so we can speculate on potential stress areas.
Although I like the idea somewhat and admire your commitment, I have to say that the approach looks terrifying. The surface quality looks much worse than an average sand casting with this wall thickness, no localised feeding is provided and mechanical properties are likely to be far below standards with these slow cooling rates. The process cannot be used for more than demonstration parts, and it is very expensive for that, as I can achieve the same effect with a painted plastic print.